By Eric Grange | April 10, 2017
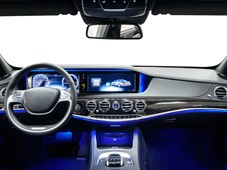
With the emergence of consumer electronics for the two last decades, our approach towards any machine has drastically changed. Indeed, with the exponential increase of computing power, many electronics products can offer the same complex functions that belonged to the ultra-expensive computers of the 1990’s.
The challenge in this situation is offering an affordable and simple interface that consumers can use to manage this complexity. Human-Machine Interfaces (HMIs) have evolved with the times, from monochrome screens with simple keyboards to the high-definition multi touch screens of today’s smartphones and tablet. This transition signifies a significant milestone in the way people control machines and the cognitive approach we have towards them. The bar has been raised and consumers expect all of their devices to have similar advanced interfaces, including the auto industry.
Car makers are facing challenges regarding the way they have to design their vehicle HMI’s because they’ve had only two vehicle platform generations to adapt. We are not yet at the level where auto engineers can remove traditional controls such as steering wheels or pedals but there are several important vehicle functions that can be digitized or automated to provide exceptional product experiences that drive sales and customer loyalty.
The influence of consumer electronics can be found in several levels in standard vehicles today:
- Screens: with the exception of very low end vehicles, almost all new cars have a color screen, mainly in the central console. Used mainly for the infotainment and navigation, these screens are used to include inputs for traditional automotive functions such as climate control.
- Screen controller: out of display, input devices should be used to manage complex HMIs. Two main options are available, depending upon the engineer’s brand and budget:
- A remote controller – a roller, touch pad is best – with a screen close to the windshield. This option is mainly used for premium vehicles because it provides a large variety of functionality within common forms such as touch pads, rotaries and push keys.
- A touch screen mounted on the dashboard is used mainly on mass market vehicles. Even cheap and reliable, this option suffers from not providing drivers with touch-feeling feedback.
- A remote controller – a roller, touch pad is best – with a screen close to the windshield. This option is mainly used for premium vehicles because it provides a large variety of functionality within common forms such as touch pads, rotaries and push keys.
- There is a huge increase in the use of button touch feel, called haptics, within the vehicle cockpit. This trend is driven largely by smartphones as people are used to working with buttons on the front or side of a device with sharp feedback. These buttons are typically short and integrating within a metallic dome.
- With the exception of a few specific brands, automakers use silicon key mats to power vehicle keys because they are a cheap, reliable and silent technology. This creates a mushy feel similar to TV remote controls and is not in line with modern consumer preferences any longer, particularly when silicon key mats travel less than 1.0mm. To improve the perceived quality of these switches, car makers should consider using dome-based systems.
C&K has provided tact switches for automakers for decades. The majority of our customers use a tact switch that is powered by a metallic dome which gives both an electrical signal and touch sensing. The reason for this decision comes from a variety of benefits the switch provides including:
- Offers a sealed system
- Can easily manage both haptics and acoustics
- No need to redevelop each unit
- Versatile PCB options
- No need for specific PCB coating
- Not reliant tied to other specific components which gives designers flexibility in their designs
- A wide variety of options for engineers to choose from
We have developed what we call “parametric haptics” which means that we can create any desired haptic by integrating different types of components, particularly within domes and actuators. C&K has found that our ability to manage the dome manufacturing process in-house gives our clients the ability to test various conditions to truly fine-tune their switches’ performance. We developed a unique manufacturing technique that creates infinite actuation and return force options up to 6.5N. These advantages give auto makers the ability to quickly develop a product fine-tuned to the specific needs of their customers.
The other big advantage of C&K’s robust manufacturing capability is the ability to evaluate haptic variations throughout the product life. We can quickly build dome prototypes so customers can try them out during the development phase. Haptics are highly subjective so this enables carmakers to test a variety of haptics to identify a component combination their customers like best. This also applies to the sound a particular switch makes. C&K has the ability to not only measure switch acoustic response but also modulate the impact through integrated manufacturing.
Automotive HMIs are entering a hybrid phase as carmakers try to strike the right balance of switch performance to suit ALL of their customers: from Baby Boomers to Millennials. Both of these groups have their own preferences so auto makers need to make sure they are catering to everyone. For now, HMIs will blend the digital and analog. It means a lower amount of switches in the short-term but more refined and engineered. C&K can help automakers and suppliers through this transition as we have the expertise and in-house manufacturing capabilities to provide high-quality components customized to exacting specifications quickly.
Eric Grange
Global Segment Manager
Automotive